When selecting flooring for environments requiring electrostatic discharge (ESD) protection, the electrical properties and material composition must be considered for durability, flexibility, and performance.
The Composition Breakdown:
30% Virgin Vinyl
Virgin vinyl is the primary component of the flooring, contributing to its flexibility and durability. Its flexibility is key, allowing for smooth installation and long-term resilience under heavy use, which is essential in environments where constant foot traffic and equipment movement are common.
40% Calcium Carbonate
Calcium carbonate is a common filler material in the production of vinyl flooring. It enhances the overall strength of the vinyl flooring and aids in providing dimensional stability. Furthermore, it contributes to the opacity and overall whiteness of the static tiles.
20% DOTP Plasticizer
DOTP (Dioctyl Terephthalate) plasticizer reduces the rigidity of the vinyl, allowing it to bend and conform to surfaces more easily. DOTP is favored over other plasticizers for its lower volatility, which ensures that the flooring maintains its flexibility over time without becoming brittle or hard. It also provides resistance to environmental stress cracking, increasing the longevity of the floor.
10% Titanium Dioxide White Paint and Additives
Titanium dioxide is widely used in the production of high-quality ESD vinyl flooring due to its exceptional whiteness, brightness, and opacity. As part of the composition, it helps to enhance the flooring’s aesthetic appeal while also providing UV resistance and chemical stability.
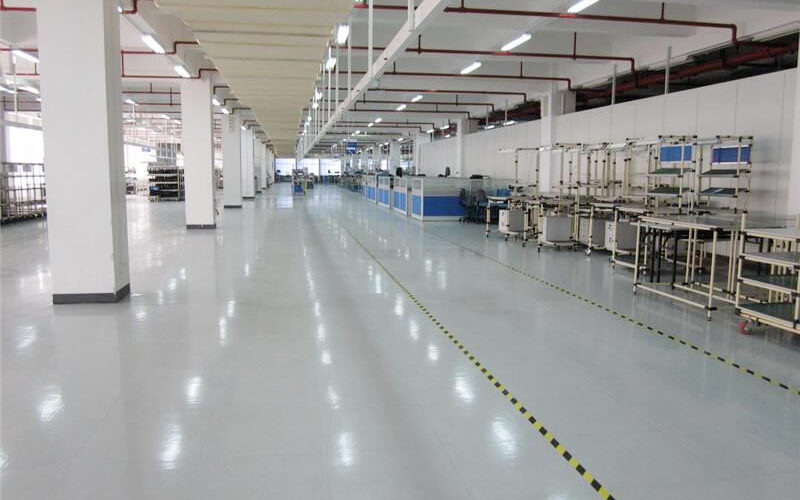
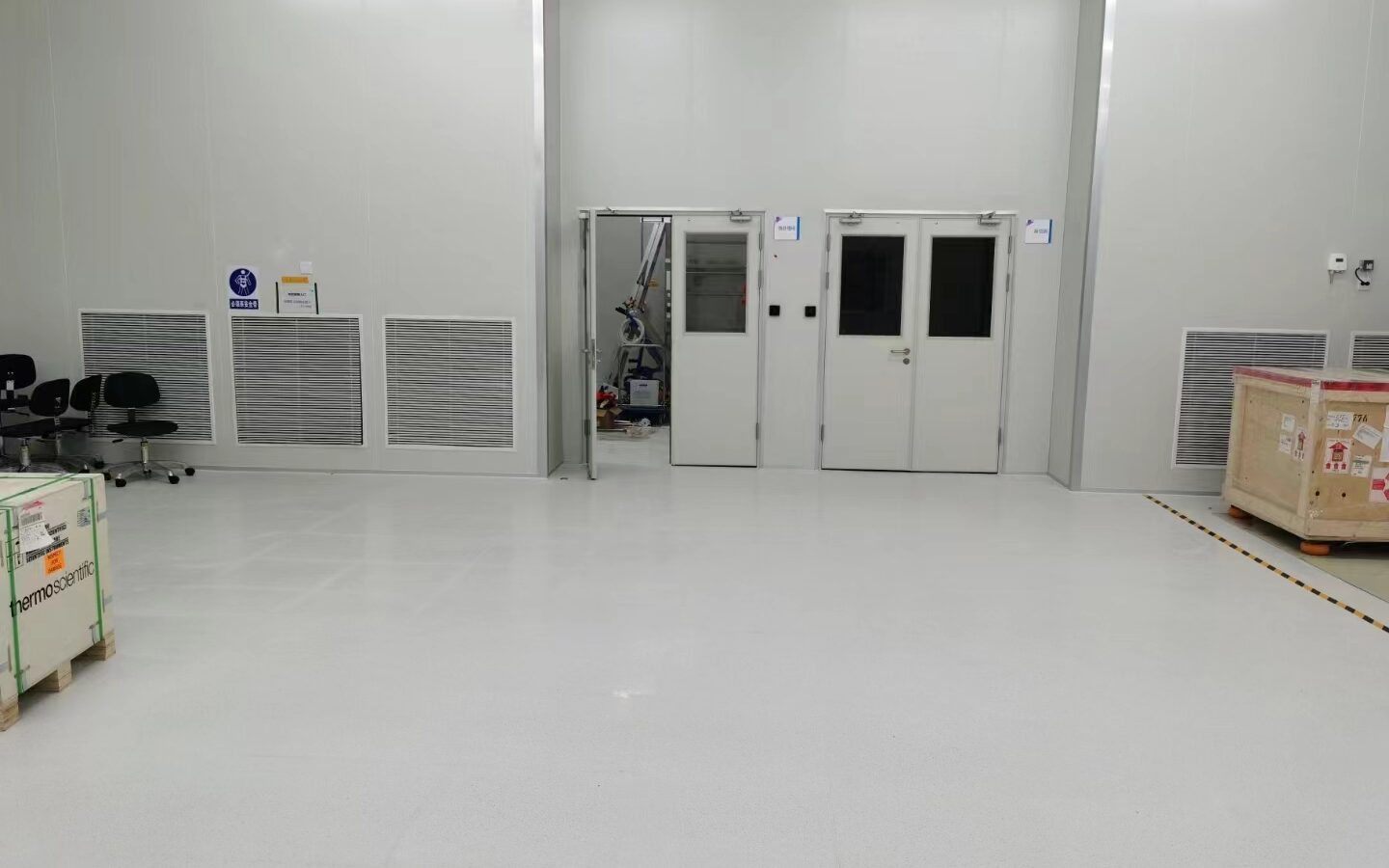
The high vinyl content ensures that the flooring is both flexible and strong, while the added materials provide enhanced protection against static build-up and contribute to a clean, aesthetic finish. Whether you’re outfitting a high-traffic manufacturing facility, a clean room, or a sensitive electronics workshop, this type of ESD flooring ensures the safety of your equipment and creates a comfortable and visually appealing workspace.